近日,就碳化硅單晶制備和碳化硅切割技術(shù)方面,有新進(jìn)展。
浙大聯(lián)合實(shí)驗(yàn)室制備出厚度達(dá)100 mm碳化硅單晶
4月26日,浙大杭州科創(chuàng)中心官微發(fā)文稱,浙江大學(xué)杭州國際科創(chuàng)中心(簡稱科創(chuàng)中心)先進(jìn)半導(dǎo)體研究院-乾晶半導(dǎo)體聯(lián)合實(shí)驗(yàn)室(簡稱聯(lián)合實(shí)驗(yàn)室)首次生長出厚度達(dá)100 mm的超厚碳化硅單晶!
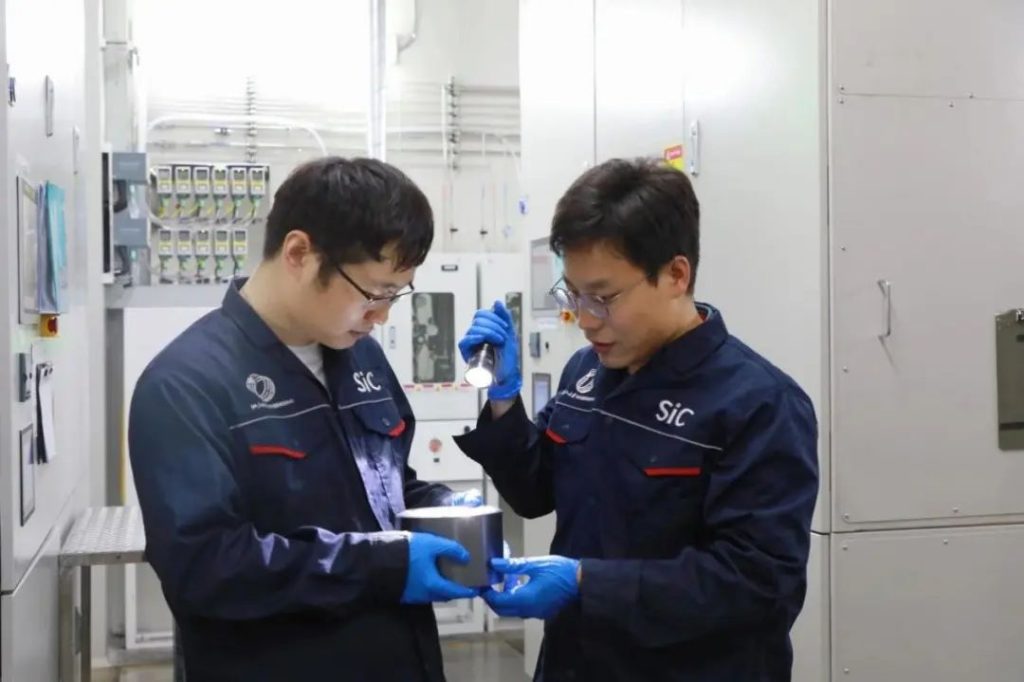
source:先進(jìn)半導(dǎo)體研究院
文章指出,為提升碳化硅晶體厚度,聯(lián)合實(shí)驗(yàn)室開展了提拉式物理氣相傳輸(Pulling Physical Vapor Transport, PPVT)法生長超厚碳化硅單晶的研究(圖1a)。
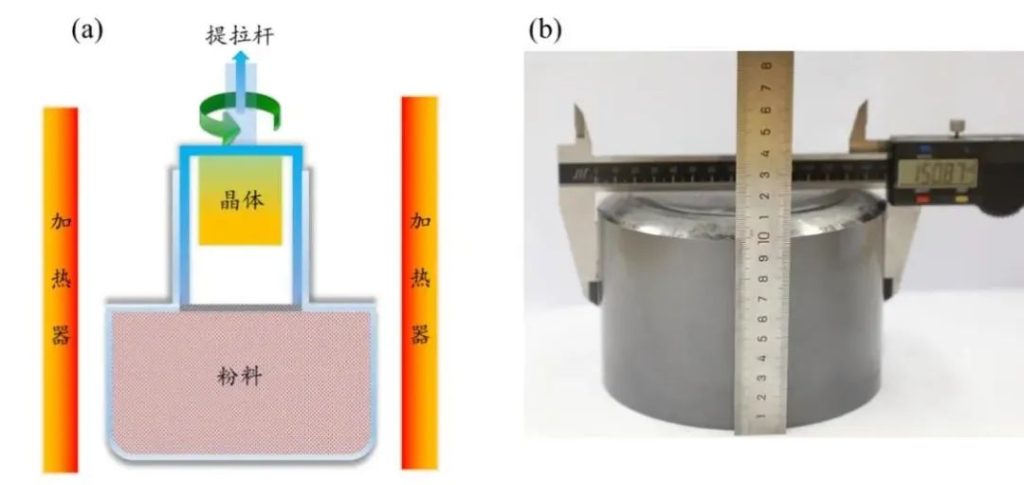
source:先進(jìn)半導(dǎo)體研究院
采用提拉式物理氣相傳輸法,聯(lián)合實(shí)驗(yàn)室成功生長出直徑為6英寸(即150mm)的碳化硅單晶,其厚度突破了100mm。測試加工而得的襯底片的結(jié)果顯示,該超厚碳化硅單晶具有單一的4H晶型(圖2a)、結(jié)晶質(zhì)量良好(圖2b),電阻率平均值不超過~ 30 mΩ·cm。
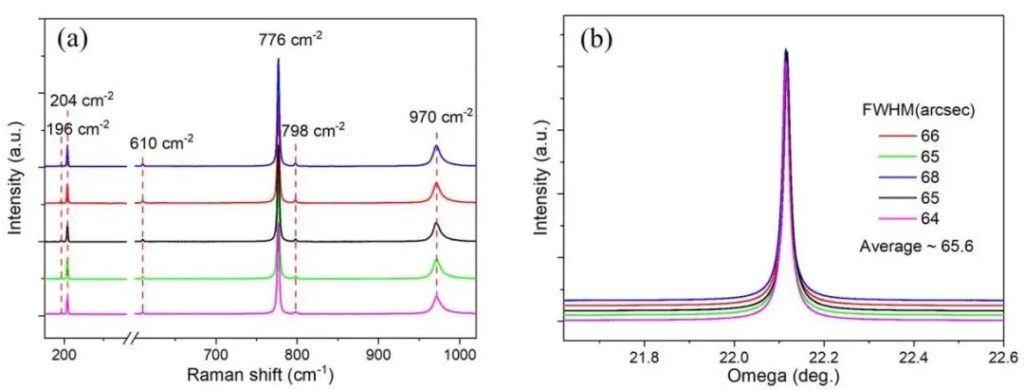
source:先進(jìn)半導(dǎo)體研究院
南京大學(xué)推出碳化硅激光切片技術(shù)
近日,南京大學(xué)成功研發(fā)出大尺寸碳化硅激光切片設(shè)備與技術(shù),標(biāo)志著我國在第三代半導(dǎo)體材料加工設(shè)備領(lǐng)域取得重要進(jìn)展。該技術(shù)不僅解決了傳統(tǒng)切割技術(shù)中的高材料損耗問題,還大幅提高了生產(chǎn)效率,對推動(dòng)碳化硅器件制造技術(shù)的發(fā)展具有重大意義。
碳化硅(SiC)作為一種關(guān)鍵的戰(zhàn)略材料,對安全、全球汽車產(chǎn)業(yè)和能源產(chǎn)業(yè)都至關(guān)重要。南京大學(xué)研發(fā)的這項(xiàng)新技術(shù),針對碳化硅單晶加工過程中的切片性能進(jìn)行了重要改進(jìn),能夠有效控制晶片表層裂紋損傷,從而提高后續(xù)薄化、拋光的加工水平。
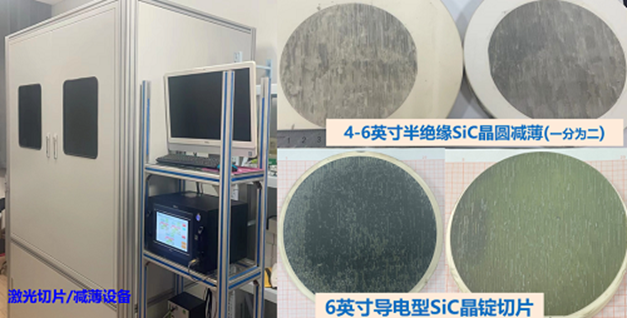
source:南京大學(xué)
“傳統(tǒng)的多線切割技術(shù)在加工碳化硅時(shí)存在材料損耗率高和加工周期長的問題,這不僅增加
了生產(chǎn)成本,也限制了產(chǎn)能。”項(xiàng)目負(fù)責(zé)人介紹,傳統(tǒng)方法在切割環(huán)節(jié)的材料利用率僅為50%,而經(jīng)過拋光研磨后的材料損耗高達(dá)75%。
為了克服這些挑戰(zhàn),南京大學(xué)的技術(shù)團(tuán)隊(duì)采用激光切片設(shè)備,顯著降低了材料損耗,并提升了生產(chǎn)效率。以一個(gè)20毫米的SiC晶錠為例,傳統(tǒng)線鋸技術(shù)能生產(chǎn)30片350微米的晶圓,而激光切片技術(shù)能生產(chǎn)50多片,甚至在優(yōu)化晶圓幾何特性后,可以將單片晶圓厚度減少到200微米,從而使單個(gè)晶錠生產(chǎn)的晶圓數(shù)量超過80片。
此外,南京大學(xué)研發(fā)的激光切片設(shè)備在切割時(shí)間上也具有顯著優(yōu)勢。6英寸半絕緣/導(dǎo)電型碳化硅晶錠的單片切割時(shí)間不超過15分鐘,單臺設(shè)備的年產(chǎn)量可達(dá)30000片以上,且單片損耗得到有效控制,半絕緣碳化硅晶錠單片損耗控制在30微米以內(nèi),導(dǎo)電型則在60微米以內(nèi),產(chǎn)片率提升超過50%。
在市場應(yīng)用前景方面,大尺寸碳化硅激光切片設(shè)備將成為未來8英寸碳化硅晶錠切片的核心設(shè)備。目前,此類設(shè)備僅有日本能夠提供,價(jià)格昂貴且對中國實(shí)行禁運(yùn)。國內(nèi)需求超過1000臺,而南京大學(xué)研發(fā)的設(shè)備不僅可用于碳化硅晶錠切割和晶片減薄,還適用于氮化鎵、氧化鎵、金剛石等材料的激光加工,具有廣闊的市場應(yīng)用前景。
來源:先進(jìn)半導(dǎo)體研究院、中國光學(xué)期刊網(wǎng)、集邦化合物半導(dǎo)體整理
更多SiC和GaN的市場資訊,請關(guān)注微信公眾賬號:集邦化合物半導(dǎo)體。